6 Ways to Reduce Maintenance Costs on Your Public Toilet Buildings
19 November 2024
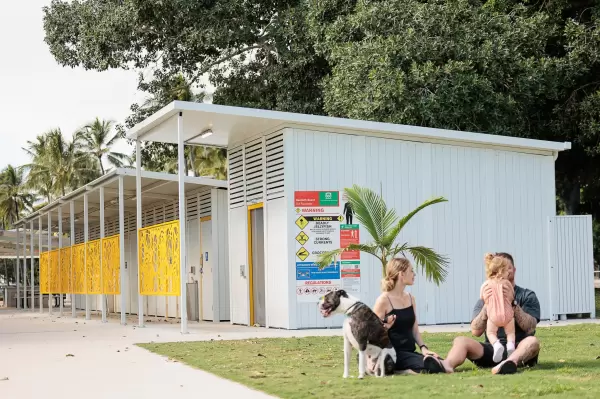
Maintenance and maintenance expenses are items that are weighing heavily upon the minds (and budgets) of a lot of Australian local councils and government organisations right now.
The cost of everything is simply getting higher.
Councils face a particular problem — they often cannot simply respond by raising rates to make up the difference.
As a result, they’re looking at the expense side of the equation to find savings.
How does this apply to toilet facilities?
Well, a large part of council's budget is maintenance. And in difficult times when money becomes scarcer, the first thing that gets looked at is maintenance.
What’s more, ongoing annual maintenance expenses of toilet blocks for councils can easily run into tens or even hundreds of thousands of dollars. That’s just cleaning and consumables. Necessary repairs from general use and wear and tear — or outright instances of vandalism — can add thousands more.
And once standards decline, that can create a cycle that discourages public use and encourages even more vandalism — research has shown that vandalism (that is not promptly cleaned or fixed) begets increasing amounts of vandalism.
Further, if you have a warranty on your facilities, neglecting maintenance can void its terms.
The good news is that both councils and the designers and architects of toilet facilities made for public use can use a variety of strategies to rein in maintenance costs.
Opt for high-quality, durable materials that able to withstand heavy use and frequent cleaning.
Public Toilets Floors Maintenance
For flooring, consider non-porous sealing options such as epoxy. These materials are not only long-lasting but also faster and easier to clean.
An unsealed concrete floor might be tempting as it costs less, but the concrete will absorb urine (and other liquids). Once ingrained, it’s very difficult to remove such odours and this can make people less inclined to use your facilities.
Some sealing finishes can also be made to look deliberately “speckled”, which reduces the prominence of dirt and scuff marks in between cleaning. This can also help you reduce maintenance frequency.

Toilet Frames and Walls Maintenance
For the frame, steel (especially if galvanised) will better resist corrosion, particularly in coastal areas where the facility will be regularly exposed to salt spray..
For walls, choose long-lasting materials that are resistant to moisture and corrosion, graffiti, and impact damage. Ribbed mini-orb panels are proven to have superior vandalism and graffiti resistance. They’re extraordinarily easy to clean and their modular nature makes them very economical to replace if damaged.
Even seemingly little things, like having gaps under the walls of your cubicles make it easier and faster for your maintenance people to wash out a facility.
The quicker they’re able to clean, the lower your ongoing operational costs.
Of course, you can use timber but it is a demanding material. It requires regular maintenance or else it will start to split and, eventually, decay. Even more durable timber imitations and finishes such as our own Modwood can prove more vulnerable to graffiti and vandalism — marks are harder to remove, and sometimes never fully removable.
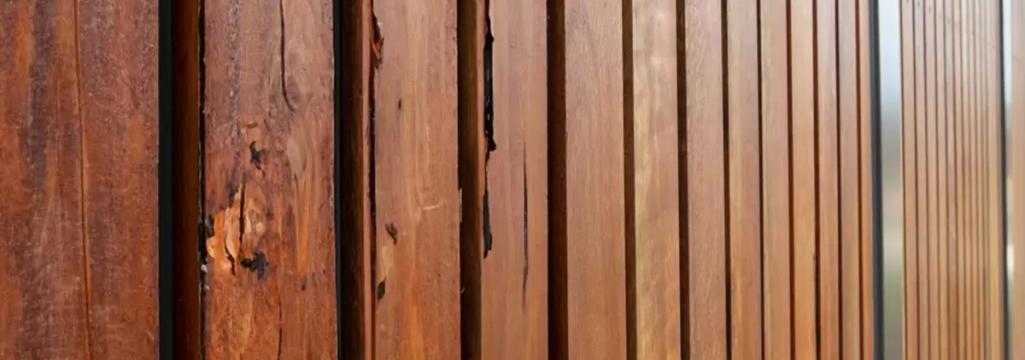
Let’s make your next project a success
Fill out the form below to start the conversation with our experienced team.
Plumbing and Fixtures Maintenance
Stainless steel pans offer the greatest longevity and the lowest maintenance since they are virtually indestructible. Stainless fixtures that have smooth surfaces also facilitate easier cleaning and reduce the accumulation of dirt and bacteria.
Wall-mounted toilets and sinks can also simplify and quicken floor cleaning processes.
Plumbing and cisterns are critical components of any toilet facility, and their design can significantly affect long-term maintenance costs. One of the best options is a centralised, hidden cistern concealed in a separately accessible service area to allow for easy maintenance and repairs without disrupting the entire facility. This approach can significantly reduce downtime and associated costs during routine maintenance or emergency repairs.
Automation and sensor technology can seem alluring, but it can easily backfire on councils. Instead of reducing maintenance costs it often seems to push them up because of the specialised nature of the repairs requires expert technicians, and very costly (and sometimes hard to source) parts.
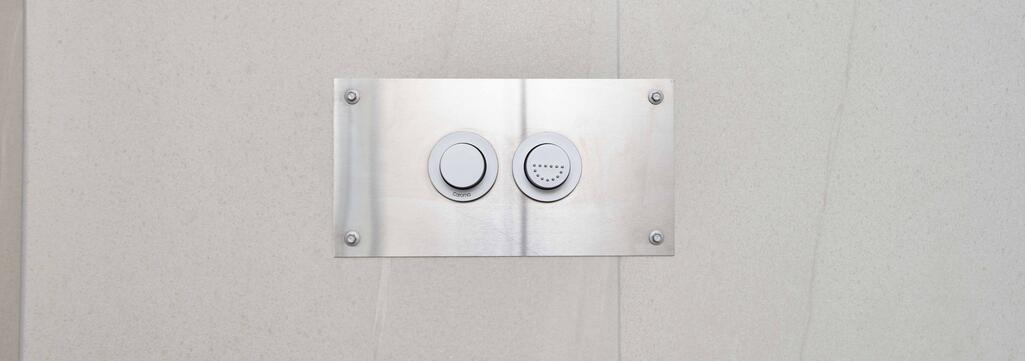
Lighting and Visibility
Natural light may also be able to be harnessed to contribute to energy savings and create a more pleasant environment. However, be mindful of privacy concerns and use frosted or translucent materials for windows or skylights.
LED lighting fixtures are standard these days due to their long lifespan and low energy consumption. The amount chosen should be sufficient to brightly illuminate the facility, and if it’s a standalone block, its surrounds. Lighting is an important factor in minimising the potential for vandalism. Well-lit facilities deter vandals by increasing visibility and fostering a sense of safety, while also helping maintenance teams quickly spot and address any damage or graffiti.
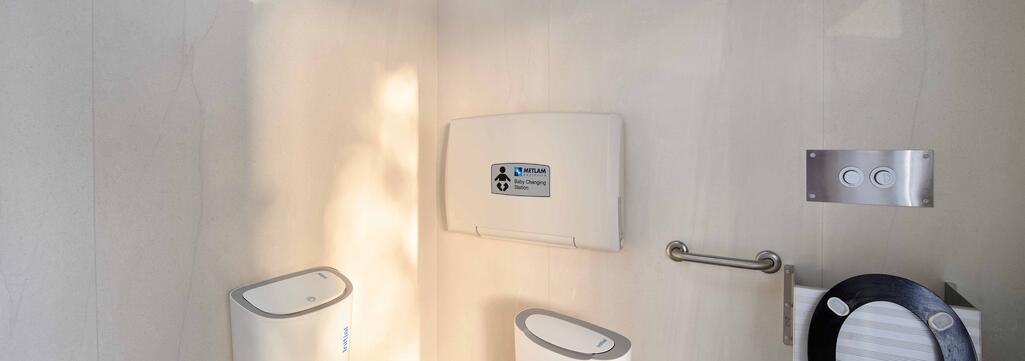
Remote toilet facilities
Remote areas bring their own special complications since there are no readily available sewerage lines to receive human waste from the facility.
Composting toilets require someone to oversee the composting process, managing solid waste, and ensuring proper ventilation to control odours — and to go “dig and stir” the waste at the appropriate time.
The challenge is that it’s not the nicest job for maintenance people, and we have found that there can be reluctance on the part of maintenance crews to perform that task — in some instances it might even be accidentally overlooked.
That has repercussions on the effectiveness of your composting solution.
A flush or long drop toilet is the alternative, with the waste then diverted into a holding tank. Later, the holding tank is emptied by a vacuum-equipped truck. Trucking out waste might seem very expensive, but there are ways to reduce the frequency that the holding tank requires emptying.
In particular, using leach trains or evaporation beds to disperse liquids will minimise the frequency that a truck is needed to remove waste —helping to ease the ongoing cost of maintenance.
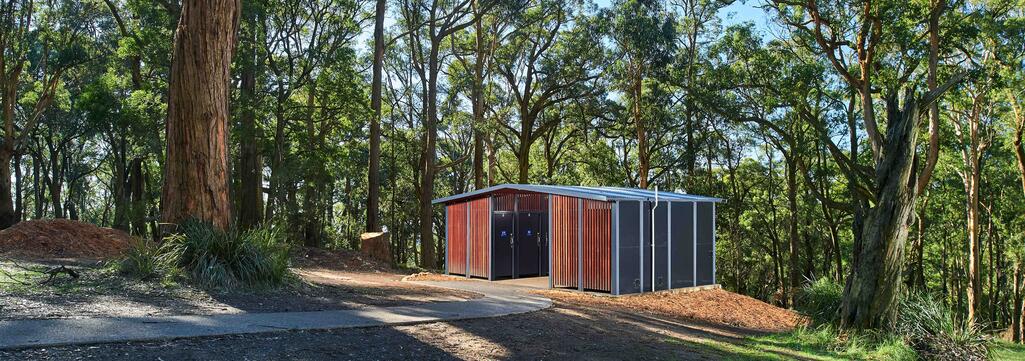
When to optimise
The best time to optimise for lower maintenance is at toilet building design. The second-best time is when you perform a refurbish. In both instances, in addition to asset and facility managers, it’s a smart idea to involve the maintenance group and seek their feedback before committing to what can be very expensive decisions.
Exploring your options with Modus
While these suggestions offer a foundation for action, it’s crucial to recognise that each project is distinct. We are experts in designing toilets for a long and useful life and low maintenance costs.
So, if you’re unsure about the best way forward, call us for a public toilet design consult on 1300 945 930 or book a project consultation below.
Have a project to do?
Planning a toilet building project can be complex but we’re here to help. Reach out or start your project consultation today.